Project Week: Royal Auping adapts production to help Dutch hospitals
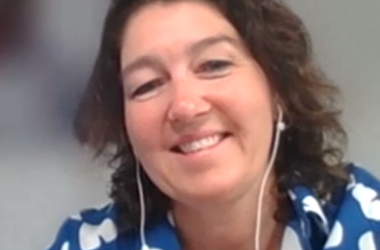
Students Get a Glimpse into How Royal Auping Adapted Production instead of Shutting down during Lockdown
Royal Auping is a family business based in Deventer that specialises in the production of beds, mattresses and box springs. The company was founded in 1888 with a mission to bring rest to the world. During this block's project week, Ine Stultjens, Manager of Marketing & Communication at Royal Auping, shared how the company adapted its production process to cope with a reduction in customer orders due to the lockdown.
What is unique about Royal Auping's production process?
Royal Auping produces only to customer orders. The company provides many options for customers to choose from, but most of their products are custom made. This allows for more efficient production and less waste. "If you only produce what the people want, you have less waste", Ine says about their production process. Care is taken to ensure all products are long lasting and the production process takes into consideration what the world should look like tomorrow. Sustainability has been in the company's DNA for a long time since they decided to take a more future-oriented approach. In the past, the company had multiple locations but merged them all into one green factory. With inspiration from the lean production in the car industry, Royal Auping took lessons on how to make its production of mattresses, beds and box springs more efficient. Consequently, teams at Royal Auping guide their work based on orders allowing them to be flexible in how they plan their work as long as delivery orders are met.
What has been the effect of the global lockdown on Royal Auping?
Royal Auping has been able to keep its factory open because the Dutch government imposed an intelligent lockdown, which allowed essential workers to continue working. The company started the year strongly with a full order book, so once the lockdown started in the Netherlands, they decided to implement their own measures. While still following their strategic plan, they also introduced a cost focus. "As the marketing & communications manager, I along with my team looked into what we could continue and what we could postpone", Ine said. Partner stores in the Netherlands remained open but in neighbouring countries like Belgium, Germany and Scandinavia stores were closed, forcing the company to survive on its Dutch orders alone.
How did the company cope with fewer orders?
By the end of March, there were many reports about the shortage of protective gear for healthcare workers, which moved Royal Auping to spring into action. The company decided to make medical FFP2 masks for medical workers in hospitals and care homes. They were then contacted by Panton, a Deventer based company that designs healthcare products. Through combining Royal Auping's expertise on working with fabric and Panton's expertise on health products, an FFP2 face mask prototype was created and certified. The prototype was shared with the Dutch government, which was enthusiastic about the quality of the product and their approach to production. This enthusiasm was matched with an order for 4 million masks.
What are some challenges Royal Auping encountered producing the masks?
Immediately after Royal Auping received the order from the government, a journalist found out and published the story bringing a lot more attention to the company. This put additional time pressure on the company to deliver its order. Collaborating with the Dutch government was a new experience that required trust from both parties as there had to be an open-book budget for the first order because the costs of production were initially unclear. Royal Auping did not have the supplies, machinery or space to begin the production of masks, so they chose to collaborate with several partners. The Dutch company DSM provided the materials needed to make the mask filters while a firm based in Arnhem provided the machines needed to make the masks. Workers had to be trained to work with the face mask fabric and the first sets of masks were made entirely by hand before the first machine was delivered. Additionally, there were a lot of sleepless nights, working at the weekend and on holidays for both Royal Auping staff and their partners in order to meet the order.
What is next for Royal Auping?
The first order of 4 million masks has been delivered and more machines are on their way. A new label has been developed, Auping Health Care, and its sticker goes on every shipment of masks. This was not a part of the company's objective but has been a result of adapting during a crisis. The company has now gone full circle as its founder, Johannes Auping, was a blacksmith who started making beds after he received an order from a neighbouring hospital. That order led him to invent the ventilating mesh bed for hospital patients and that spirit of innovation lives on today. This crisis has shown the importance of flexibility and constantly being on the lookout for different opportunities.
WUP 10/6/2020
by Olivia Kawuma
©WUAS Press